Abstract
The physical and mechanical characteristics of hollow polyester fibers were compared with solid polyester fibers in order to establish their processing behaviour and performance characteristics. The effects of hollow fibers on fabric properties were investigated by using microscopy and tests of tensile and bursting strength, pilling, abrasion resistance, water vapour permeability, and handle.The results show that tensile strength of hollow polyester fibers and yarns are negatively affected by the cavity inside the fibers . Hollow fibers also have higher stiffness and resistance to bending at relaxed state. Fabrics made from hollow polyester/wool blends and pure wool fabrics show three distinguishable steps in pilling. During pilling, hollow fibers break before being pulled fully out of the structure, leading to shorter protruding fibers . Microscopy studies showed that the breakdown of hollow fibers started during entanglement by splitting along the helical lines between fibrils. KES results showed that the friction between fibers and the fibers shape are the most important parameters that determine the fabric low stress mechanical properties. However, in some aspects, the hollow structure of the fibers does not have a significant effect.Keywords: Hollow fibers , Knitted fabric, Pilling, Wool/polyester, Mechanical property
Introduction Hollow fibers production by changing the shape of the spinning nozzle is a physical modification of polyester (PET) during fibers production to achieve new properties
Synthetic fibers for general commercial application are mostly solid filament or solid fibers yarns. Hollow fibers have benefits for specific applications due to the larger fibers surface/volume ratio [1]. A change in the shape of the cross-section in man-made fibers affects many physical characteristics such as sorption, dyeability, touch, pilling resistance, abrasion, weight, bulk, thermal properties, insulation capacity, glistening, lustre, covering and opaqueness.
Fibers cross-section shape also affects the fabric hand and the changed hand of the hollow fibers can be conveniently utilized in wool/polyester blended yarns. Furthermore, hollow fibers must have sufficient mechanical qualities for the selected end uses. In this research, the natural properties of wool are combined with hollow polyester fibers to develop novel products with enhanced performance.
In this paper, the results on the fabric mechanical properties and fabric hand are presented.
Experimental Solid and hollow polyester fibers (hole diameter to fibers diameter ratio of 25%), and Super-wash treated wool were supplied and spun by Bulmer & Lumb, Bradford, UK. Yarns were knitted using Stoll weft flat knitted machine in the University of Manchester. The material properties are listed in Table 1. The yarns were top-dyed commercially with different colours using HT methods by Bulmer & Lumb. It is noteworthy that the yarn samples were manufactured in industrial scale. Therefore, chosing hollow and solid polyester fibers fabrics with the same shade was unfortunately impossible. Sodium carbonate (from Tennents) and non-ionic detergent, Alcapol NFC (from Ciba) were used for washing and relaxation of the knitted fabrics. The knitted samples were washed with a 0.5 g/l non-ionic detergent, pH 8-9 (sodium carbonate) at 40-50 ºC for 30 minutes. The fabrics were then washed off at 35-40 ºC for 45 minutes and cooled gradually, and finally rinsed cold and air dried without any tension. Fabric mechanical properties were compared by measuring fibers and yarn tensile strength, yarn-on-yarn dry abrasion, fabric bursting strength, pilling, abrasion resistance, hand, and water vapour permeability. Fibers topography was analysed after pilling and abrasion tests using SEM (Hitachi S-3000 N). Fibers tensile testing was performed in accordance with BS 3411:1971 on an Instron 5564 with a sample length of 20 mm and crosshead speed of 10 mm/min. Breaking force and elongation at break of yarns were measured according to BS 2062:1995, with gauge length of 250 mm, crosshead speed of 250 mm/min, and 50 tests for each sample. The results of tensile tests are reported by confident limit of 95 %. Yarn-on-yarn abrasion resistance was evaluated by equipment built at the University of Manchester.
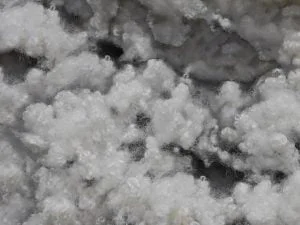
The test essentially involves subjecting two yarn sections, wrapped helically together, to a reciprocating motion under tension until failure.
1999 on a Mullen Burst Tester with sample area of 50 cm2 , 20 seconds time to burst and 10 tests per sample. The pilling ratings were studied according to BS 12945- 2:2000 by a Martindale Abrasion Tester on scoured and relaxed sample under 9 KPa pressure and different number of rubs including 125, 500, 1000, 2000, 5000, and 7000. Pilling resistance was determined by comparison with standard pictures in a light cabinet. The abrasion resistance was measured on a Martindale Wear & Abrasion Tester according to BS 12947-2: 1999. The mass loss during abrasion was measured according to BS 12947-3: 1999 on scoured and relaxed samples under 9 KPa pressure.
The occurrence of one broken thread (observed under Vickers Zoomax Light Microscope) was considered as the end point. It should be mentioned that when pilling was observed on the specimen, the test was continued without cutting off the pills. The fabric hand was tested using the Kawabata Evaluation System (KES). Four tests were carried for each KES parameter. Water vapour permeability of fabrics was carried out in accordance with BS 7209-1990 using an Equiptex Water Vapour Permeability Tester on conditioned samples. The water temperature was 20±2 ºC and its surface height to fabric was 1 cm. After establishing equilibrium (1 hr), weight measurements were done after 6 and 24 hrs. The Water Vapour Permeability (WVP) in g/m2 /day was calculated by the following formula: WVP = 24M/At (1) Where M is the loss in mass of the assembly over the time period t (in g); t is the time between successive weighing of the assembly (in hr); A is the area of exposed test fabric (internal area of the test dish) (in m2 ).
The Water Vapour Permeability Index is given by: I = {(WVP)f / (WVP)r}×100 (2) Where (WVP)f is the mean Water Vapour Permeability of the fabric under test; (WVP)r is the Water Vapour Permeability of the reference fabric (a high tenacity polyester woven with monofilament). Results and Discussions The tensile properties of hollow fibers are compared with those of solid fibers in Table 2. Hollow fibers tend to have lower tenacity, with the other tensile properties affected by the dyeing process, high temperature top dyeing. In particular the black fibers appear to have lower tenacity but higher elongation. Yarn and fabric properties are shown in Table 3.
Solid fibers blended yarns have the highest tenacity while the pure wool yarn has the lowest tenacity. As can be seen the yarn produced from hollow fibers have lower tenacity and wear resistance. The reason for the differences in tenacity will be discussed further along with the pilling results. The lower resistance to abrasion of the hollow fibers yarns may be attributed to the higher surface friction of the hollow.
fibers , or to the greater contact area or inherent weakness of the hollow fibers [2,4,9]. The pure wool fabric has much lower bursting strength in comparison with polyester/wool blended fabrics. This is likely due to the greater elongation of the blended yarns.
During the bursting strength test, fabric starts to fail from the direction with the lowest breaking extension. The reason for this phenomenon is that, when the fabric is stressed in all the directions in the test, the fabric direction with thr lowest elongation at break is the one that will fail first. Consequently, this direction is not necessarily the direction with the lowest strength. Therefore it was expected that the wool fabric would have the lowest bursting strength as it has the lowest extension. In addition, using hollow polyester fibers increased the fabrics bursting strength significantly as compared with the pure wool fabric. The fabric pilling performance is compared in Table 4. At low levels of mechanical action, no pills formed and the only visible change was fuzz formation.
After 500 rubs, however, the entanglement phase started, with pills forming. After higher mechanical abrasion, the apparent pilling was reduced and with pill removal becoming the predominant process. These three steps can be clearly seen for samples composed of 100% wool, and the hollow polyester/wool fabrics with dark blue and brown colours. Also the results show that the hollow fibers samples have lower pilling tendency and higher rate of pill wear-off than solid fibers samples. The differences between the two types of polyester fibers can be seen in Figures 1 to 5, with Figure 1 indicating the high pill density of solid polyester fibers fabrics resulted from the high abrasion resistance and strength of polyester fibers .
The solid fibers fabrics are less affected by the pill wear-off. Although some wool fibers can be observed in the pills, the main component is polyester, with multiple fibers splitting fatigue resulting in the wear-off of the wool fibers . With hollow fibers having lower strength than the solid polyester fibers , the associated effect is that pill wear-off is faster for hollow fibers . After 5000 rubs, their pilling appearance is clearly better (Figure 2, as compared with Figure 1). It was reported that the greater the breaking strength and Table 4. Pilling performance of knitted fabrics Sample \ number of rubs 125 500 1000 2000 5000 7000 Average SP/W Black 5 4 3-4 2-3 3 2-3 3.5 SP/W Charcoal 5 5 3 2-3 1-2 1 3.0 HP/W Brown 5 5 4-5 3-4 5 5 4.7 HP/W Charcoal 5 5 4-5 3-4 4 4 4.3 HP/W Darkblue 5 4-5 4-5 3-4 4-5 5 4.5 Wool 5 4 3-4 4 5 5 4.4 Figure 1. Pilling of solid polyester/wool fabrics after 7000 rubs. High pill density on the fabric surface is evident with solid polyester fibers as a main component, with multiple wool fibers splitting resulting in the wear-off the wool fibers .
Figure 2. Pill wear-off on the surface of brown hollow polyester/ wool fabric after 5000 rubs.
the lower the bending stiffness of the fibers , the more likely they can be pulled out of the fabric structure and producing long protruding fibers .
But hollow fibers with lower breaking strength and high bending stiffness will tend to break before being pulled fully out of the structure leading to shorter protruding fibers (Figures 3, 4). This means that many protruding fibers can not reach the “critical height” for the for fibers entanglement and pill formation. The break down of hollow fibers commences during entanglement by splitting along the helical lines between fibrils and is continued along the fibers axes and finished with bushy ends (Figure 5). The fibers break develops along the axial splits, due to either repeated bending, or bending and twisting (Figure 6). Also, the individual portions of the split can break to give many splits (Figure 7). Furthermore, the axial splits can occur from tensile fatigue (Figure 8), or peeling by surface shear, failure by surface wear creating peeled fibers (Figure 9).
The other type of fibers break down can be found in Figure 10. Figure 10(A) shows a wool fibers with a split end; Figure 3. Pill wear-off on the surface of charcoal hollow polyester/ wool fabrics after 7000 rubs. Figure 4. Breakage of hollow polyester fibers during entanglement. (A) charcoal and (B) brown hollow polyester/wool fabrics after 5000 rubs. Figure 5. Breakage steps of brown hollow polyester fibers after 5000 rubs. (A) start of fibers breakage along helical lines between fibrils, (B-H) continued splitting along the fibers axes, and (I) bushy end of breakage.
Figure 10(B) shows a failure adjacent to a knot which is likely to be caused by flexural fatigue. As can be seen from Figures 4 and 5, splits along the hollow polyester fibers can be extremely long. This is a consequence of the fact that the axial crack in this fibers type runs much more closely parallel to the fibers axis. The phenomenon is a characteristic of the highly oriented, highly crystalline, linear polymer fibers .
Figures 11 and 12 show the tensile breakage of hollow and solid polyester fibers respectively. It is clear that the tensile strength of hollow polyester fibers is adversely affected by the cavity inside the fibers which acts as a weak point where the failure can be initiated. In the case of wool which has low breaking strength, pills will be easily removed and detached from the fabric. But for fabrics containing solid polyester fibers , the pills will tend to remain in place. Therefore, even after 7000 rubs their pilling ratings are quite high. In conclusion it can be stated that the higher the tensile strength and abrasion resistance of the fibers , the higher the pilling tendency of the fabric. This is mainly controlled by pill wear-off.
The results of abrasion test, Table 3 and Figure 13, show the significant effects of fibers type. The ability of a fibers to resist repeated distortion is very important to its abrasion resistance. Therefore high elongation, elastic recovery and work of rupture are considered to be the key factors for a good degree of flat abrasion resistance in a fibers rather than high strength.
Polyester fibers are considered to have good abrasion resistance and a comparison of the hollow and solid polyester fibers indicated that the hollow fibers have lower abrasion resistance, which may be related to their shape. Compared with solid fibers of the same linear density, hollow fibers are stiffer, more resistant to bending and torsion and have a relatively poor resistance to flexural strain [3,9]. Therefore they abraded faster than the comparable solid polyester fibers . Measuring the mass loss during abrasion also demonstrated the higher rate of hollow fibers removal during abrasion (Figure 13). While these fibers were broken between 15,000 to 24,000 rubs, the minimum abrasion for solid fibers was 37,000 rubs. Furthermore, it is evident that the dyeing processes have a significant effect on fibers properties. The abrasion resistance of hollow polyester/wool fabric with dark blue colour is at least 8000 rubs higher than similar samples with the charcoal colour which may be related to the dyeing period at high temperature. The mass loss during abrasion is also compatible with the rubs to break; a higher weight loss during abrasion correlates to a lower number of rubs to break.
The results also revealed the great improvement of wool abrasion resistance by blending with hollow and solid polyester fibers . KES-F mechanical properties of knitted fabrics before and after relaxation were measured. The results indicate that after relaxation, there is an increase in extension (EM) for all the samples (Tables 5 and 6). In general extensibility of the solid polyester fibers samples are higher than the comparable samples based on hollow fibers . The changes in these properties indicate that the friction between fibers has been reduced by the relaxation shrinkage process which makes fabrics more extensible with better elastic recovery. But the differences between hollow and solid polyester fibers show that the friction between solid fibers is lower than hollow fibers which can be related to the shape of fibers , because in general these fibers have greater outside surface area, resulting in a greater frictional contact area.
The tensile properties of the wool fabric changed greatly after relaxation. The EM and RT (recovery) increased significantly. However, blending wool with polyester fibers especially hollow fibers reduced the effects of relaxation on the tensile properties. It is expected that bending rigidity and bending hysteresis of all the samples will decrease after scouring, but the grey samples were so unstable that it was impossible to measure their bending properties accurately. The results from the relaxed samples clearly show that the bending stiffness of hollow fibers fabrics is much higher than that of the solid fibers fabrics. These hollow fibers have the same linear density as the solid fibers , therefore, they are stiffer and more resistant to bending and torsion [44,12].
The shear properties of all the samples were reduced by scouring. This is mainly due to decreasing inter-yarn friction. In general, shear rigidity and hysteresis of hollow fibers fabrics are greater than solid fibers fabrics. The effects of different colours during dyeing on shear properties are not significant because the dyeing operation generally produced fabrics with low yarn interactions regardless of colour. Relaxation shrinkage decreases the friction coefficient (MIU) and its variation (MMD) of polyester/wool blend fabrics. This may be due to the tighter and more compact structure of the fabrics after shrinkage making the gaps in the fabric and the surface variation smaller. The surface roughness (SMD) of hollow fibers based fabrics increased after scouring while the solid polyester/wool fibers fabrics showed lower surface roughness.
The larger diameter and higher bulk of the hollow fibers produce result in higher SMD, demonstrating that the fabric hand is dependent on fibers cross-section. It is generally expected that fabrics have higher energy of compression (WC) after scouring, but here the trend is decreasing.
This may be due to the more compact structure after relaxation. The recovery after compression (RC) of all the samples increased. This is compatible with the reduction of friction between yarns and fibers due to the release of internal fabric tension. As already mentioned hollow fibers have more friction, consequently fabrics with these fibers have lower RC. In any relaxation process the thickness of fabrics increases. This is shown in this study as well. Also, it was found that the thicknesses of hollow fibers fabrics are higher than that of the solid fibers fabrics. Clearly, the increased fibers external dimension of the hollow fibers is a factor. In fact, the greater fabric thickness is one of the reasons to use hollow fibers as this leads to greater thermal insulation.The permeability to water vapour, the thermal insulating, and water transport are some of the basic factors affecting thermal comfort. These properties can be influenced by suitable choice of fibers cross-sectional shapes, the formation of cavities or micro-cavities in the fibers and other modifications to fibers geometry. They can also be influenced by fibers blending and fabric construction [3]. The results of water vapour permeability tests, Table 7, indicate that relaxation resulted in a more compact structure and consequently a reduction in the water vapour permeability of fabrics. This effect is greater than the influence of the type of fibers . In this aspect, fabric and yarn structure is more important than the constituent fibers . Conclusion Solid polyester fibers fabrics have higher tensile and bursting strength, and better abrasion resistance.However, by using hollow fibers in the fabrics, the extent of pilling, a serious fabric appearance defect for high strength synthetic fibers fabrics was reduced by about 40%, a result of faster pill wear-off, due to the differences in the physical properties of the constituent fibers . The use of hollow fibers resulted in lower extensibility, tensile and compressional resilience, greater bending and shear stiffness and hysteresis. Accordingly the results indicate that by using hollow fibers , it is possible to produce a fabric similar to that base on solid polyester fibers but with higher stiffness and rougher texture. The fabric and yarn structures control the overall fabric handle and water vapour permeability. The use of hollow fibers increases fabric thickness.This should increase the thermal resistance. Acknowledgements Financial support of the Iran’s Ministry of Science, Research and Technology, and Bulmer & Lumb Company to afford fibers and yarns is gratefully appreciated.